Are you wondering where your new order disappeared to? You’re certain you didn’t sell all of it, but when you check your inventory, it isn’t there. You could be dealing with inventory shrinkage.
Inventory shrinkage, the unexpected loss of inventory, is a big problem in retail. It accounted for roughly $100 billion in losses in 2022—up from about $90 billion in 2020.
Luckily there are steps that you can take to help reduce shrinkage.
What Is Inventory Shrinkage?
Inventory shrinkage is when your actual inventory is lower than what your books say it should be. This can happen due to theft, supplier error or fraud, product damage, human error while counting inventory, or other reasons.
Some shrinkage is expected for any retail store, but you want to keep an eye on just how high your shrink is, as it can reduce your profits.
The average inventory shrinkage rate across all industries was 1.4% in 2022, but if you work in the food industry, for example, where inventory is more likely to spoil, this rate could be higher.
Inventory shrinkage is considered an expense that affects both your balance sheet (specifically the inventory account) and your income statement (unless the amount is small, and then it can be included under the cost of goods sold).
To find out how large your inventory shrinkage is, you’ll need to calculate it. Then you’ll know how best to expense it for your business and whether you need to take steps to reduce it.
How Do You Calculate Inventory Shrinkage?
Step 1
First, you need to figure out how much inventory your books say you have. This is known as your recorded inventory.
To do this, subtract the cost of goods sold (all of the costs, including labor, materials, and overhead associated with selling an item) from your inventory. This gives you the book value of your inventory.
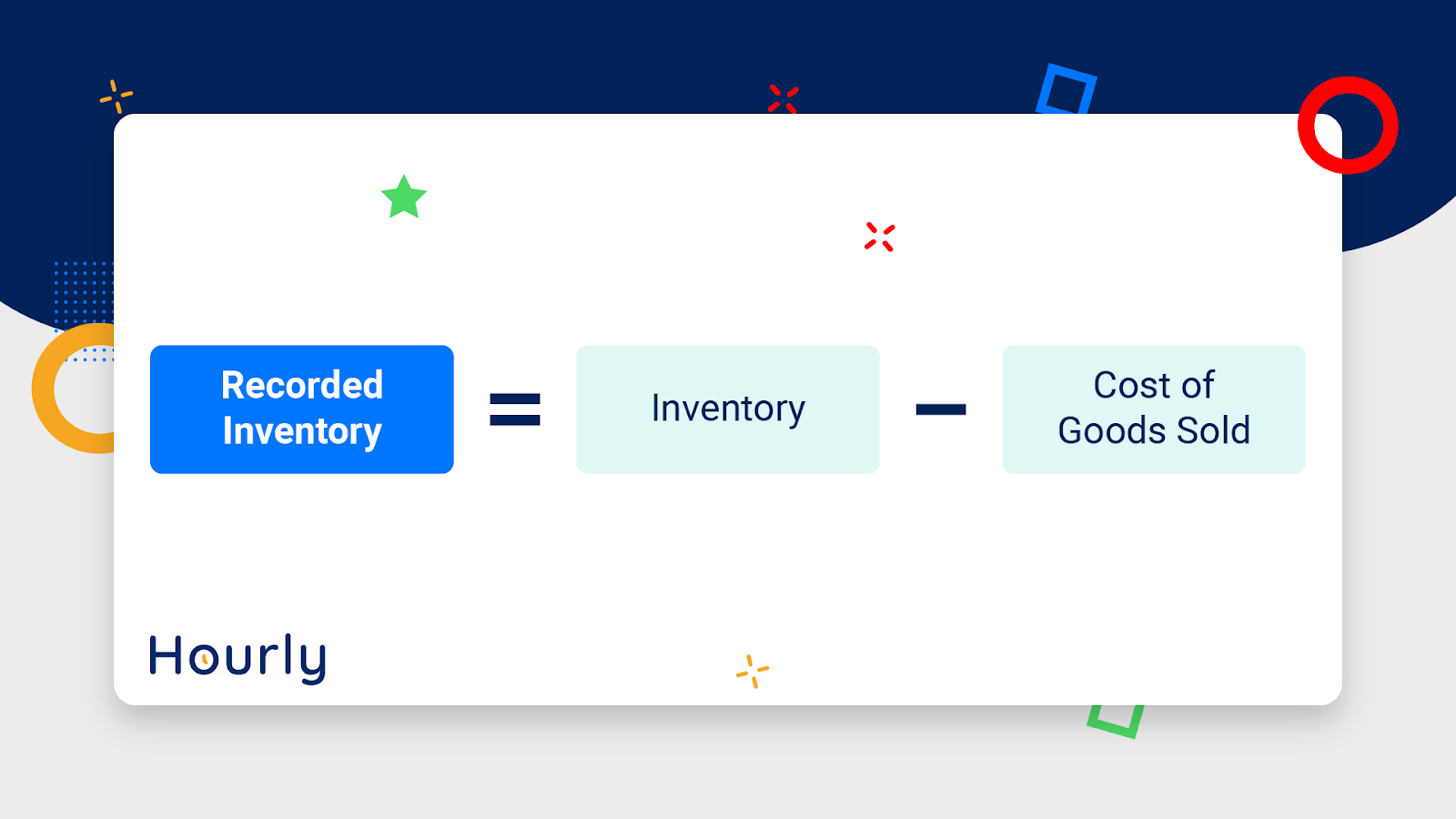
Step 2
Now that you know the recorded amount of inventory you have, it’s time to do a physical count of your inventory to see how much you actually have. This is your actual inventory. In a perfect world, it would be exactly the same as the recorded inventory listed in your general ledger.
Step 3
With these two values in hand, you’re ready to calculate your inventory shrinkage, which is your recorded inventory minus your actual inventory.
Inventory Shrinkage = Recorded Inventory – Actual Inventory
If your actual inventory is smaller than your recorded inventory, you have shrinkage.
Step 4
The last step is to calculate how much your inventory has shrunk by. This is your inventory shrinkage rate. Here's the formula:
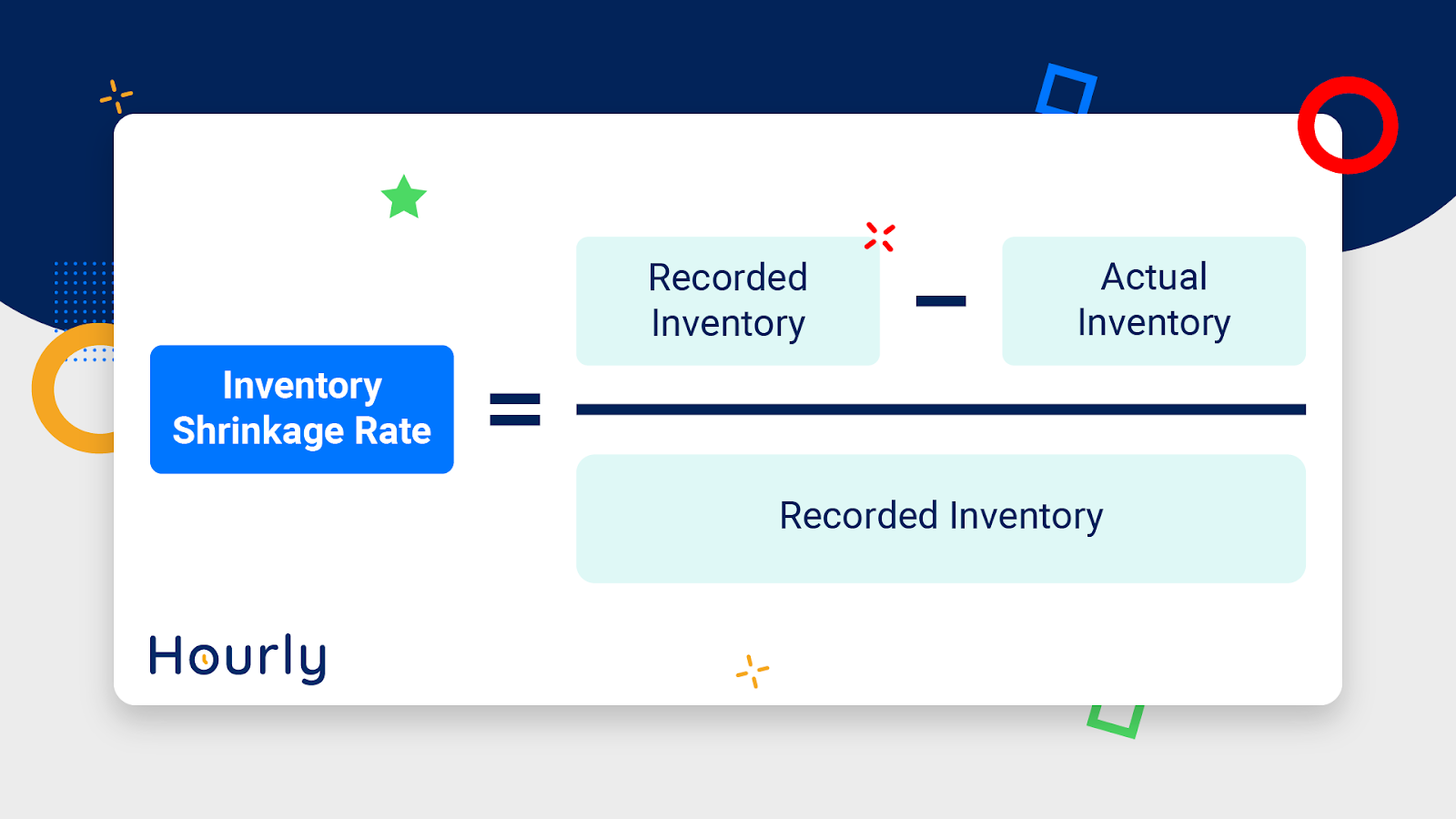
With your inventory shrinkage percentage, you now know the rate at which your inventory is being lost for reasons outside of sales.
Ready to transform your business into a profit-pumping machine? Learn how with our monthly newsletter.
Subscription implies consent to our privacy policy.
An Example of Inventory Shrinkage
Let’s say you run a small cafe. Your inventory management software shows you should have 50 lbs. of coffee that you purchased for $5,000 left in your inventory. This is based on how much you had at the beginning of the month and how many cups you sold.
But, you do a count and find 49 lbs. of coffee, with a value of $4,900 left. You’d like to know how much of your inventory is a loss, so you decide to determine your inventory shrinkage rate.
To calculate that, you’ll need the inventory shrinkage rate formula we mentioned above:
- Inventory Shrinkage Rate = (Recorded Inventory – Actual Inventory) / Recorded Inventory
Here’s how to use the formula to find the shrinkage rate:
- ($5,000 – $4,900)/$5,000
- = 0.02
- Multiply 0.02 by 100, and you get a shrinkage rate of 2%.
While $100 may not seem like a lot in the grand scheme of things, it does represent 2% shrinkage, which is above the 1.4% average shrink found in retail sales. If it continues long-term, say every month for 12 months, it could lead to a serious loss in profits.
What Causes Inventory Shrinkage?
There are a few main causes of inventory shrinkage. The likelihood and severity of each of these will depend on your industry.
External Theft
External theft, like shoplifting, is one of the largest causes of shrinkage reported by retailers, accounting for 37% of all shrinkage.
One of the biggest threats in this category is organized retail crime (ORC), which are groups that steal large amounts of inventory to sell online.
Unlike individuals, they go after a wide variety of goods, from raw materials to electronics and other commodities.
According to one study, 67% of asset protection managers reported a moderate to considerable increase in ORC. And 80% of those surveyed believed that the issue would only get worse.
Employee Theft
Internal theft accounts for 28.5% of shrinkage, according to the National Retail Federation. This sort of shrink can come in the form of embezzlement, skimming, larceny, or more elaborate schemes. It may involve only one employee, or it could include a small group of workers.
These problems often occur over a number of years. One recent case that made headlines was a school food service director who stole $1.5 million worth of food, mostly chicken wings, over a few years. The scam was uncovered during a routine mid-year audit, highlighting the importance of regular checkups.
Another way you can lose money from workers is with employee time theft. That’s why employee payroll software like Hourly is so important since it automatically tracks your workers’ hours.
Vendor Fraud
This type of inventory shrinkage can include things like miscounting shipments, falsifying deliverables, or intentionally sending incorrect inventory.
For example, let’s say you ordered 100 lbs. of a specific breed of tulip bulbs for your greenhouse. Unfortunately, after a few months, you realize only half of the flowers were as described, and the rest either didn’t bloom or were a different, less valuable variety.
This is a pretty common form of vendor fraud, but checking your inventory reports can help you catch it before it grows into a bigger problem.
Product Damage or Error
Miscounting, poor record keeping, and damage can also add to your shrink rate. For restaurants or other food industry businesses, this includes issues like spoilage.
If your staff members aren’t following the first in, first out (FIFO) inventory policy as closely as they should, this could be contributing to the problem. For example, if your chef grabs the closest onions, even if an older shipment is sitting in inventory, those older onions might end up rotting before they can be used.
One study found that 4-10% of all food in restaurants never reaches customers.
By following proper inventory usage protocols, like FIFO, product damage or spoilage can be one of the easiest forms of inventory shrinkage to prevent.
How To Prevent Inventory Shrinkage
While some inventory shrinkage usually happens at any business, you can prevent it from making a huge dent in your profits by using these strategies:
- Inspect your deliveries: Don’t make assumptions. This includes carefully checking all new orders or when you reorder a product. You might find instances of damaged products or inaccurate counts. By checking these yourself, you have a better chance of not being overcharged for these inaccurate deliveries.
- Conduct more frequent inventory checks: While it might be common to do a year-end inventory count for tax or audit purposes, doing counts more frequently can help you catch issues and errors before they blow up.
- Checks and balances: Don’t ask an employee to check your inventory records alone, no matter how trusted. Instead, have them work in teams and encourage them to report any suspected theft or fraud.
- Double-check everything: Even if you use an inventory management system, don’t assume because your inventory is counted by a computer that it’s always accurate. Consider doing physical counts frequently to verify your system is working as expected.
- Consider switching your inventory valuation method: It may be time to switch to something like specific identification (where you track each item exactly), especially if you're using the weighted average cost method, which assigns an average cost to your inventory.
- Consider strict adherence to FIFO and other spoilage prevention policies: For some businesses, like restaurants or supermarkets, discounting food that is approaching its sell-by date could help.
- Have a well-documented return policy: This will help prevent customers from returning stolen goods. Something simple like requiring a receipt can help since stolen items won’t have one.
- Ask employees to monitor customers: A simple “hello” to shoppers entering your store can help deter shoplifting. It lets customers know that your staff is alert and ready to provide customer service and keep an eye on any would-be thieves.
- Consider adding cameras: Point of sale (POS) video analytics, especially at self-checkouts, are becoming more popular. According to data collected by the National Retail Federation, nearly 30% of retailers said they had or planned to implement the technology to help with loss prevention.
- Use radio frequency identification (RFID) systems: RFIDs are small devices that use radio waves to track items, and they can go much farther than older security tags.
How you choose to deal with inventory shrinkage will depend on your industry, budget, and the type of shrinkage affecting your business the most. This is why keeping track of your inventory and having a good understanding of what’s happening in your stores is so important.
For instance, if you install a new video surveillance system in your stores, but your real issue is in your supply chain or warehouse management, you won’t see any meaningful change to your bottom line.
Use What You’ve Learned to Reduce Inventory Shrinkage
If you perform frequent inventory audits and talk to your team, you’ll often get a better overall idea of where the shrinkage is coming from. Once you know what the problem is, you can take steps to get it under control.
It may be impossible to reduce inventory shrinkage completely, but with careful accounting records, honesty, and security measures, you can limit waste and theft.